Liquid Silicone Injection Molding Services
Liquid Silicone Injection Molding (LSIM) is a versatile manufacturing process that involves injecting a liquid silicone compound into a heated mold, where it cures to create a final part. This process offers numerous benefits across various applications due to its flexibility, durability, and resistance to high temperatures.
Key Characteristics of LSIM
- Precision Molding: Liquid silicone is injected into a heated mold for accurate shaping.
- Chemical Curing: The compound cures when combined with a catalyst in the mold.
- Permanent Shape Retention: Ideal for applications where parts must maintain their shape and properties over time.
Advantages of Liquid Silicone Rubber (LSR)
A key benefit of liquid silicone injection molding is the ability to produce parts with complex geometries and features, such as those found in drug delivery products or medical devices. LSR allows molding of intricate shapes that are challenging or impossible to achieve with traditional methods like thermal or compression molding.
LSR is a thermosetting polymer, meaning its molded state is permanent. Unlike thermoplastics, it cannot be melted and reshaped, making it ideal for long-lasting applications in medical and industrial settings.
Applications of LSIM
LSIM is a versatile technology with a wide range of applications across various industries. Two common areas where we utilize this technology:
Medical Applications
- Diagnostic equipment
- Surgical instruments
- Pharmaceutical equipment and packaging (e.g., stoppers and seals)
Baby Products
- Anti-colic valves
- Other baby-related items
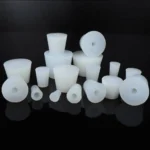
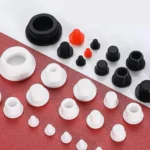

Key Features and Capabilities
Equipment
Handles high-viscosity materials, producing complex parts with intricate details.
Materials
Liquid Silicone Rubber (LSR) exhibits:
- High-temperature resistance: Up to 250°C (482°F)
- Low-temperature flexibility
- Chemical resistance: Resistant to fuels, oils, and cleaning agents
- Biocompatibility: Suitable for medical devices and implants
- High transparency: Useful for visibility or optical clarity
Formulations
Variables such as:
- Cure time
- Elastic modulus
- Tensile strength
These properties can be adjusted to tailor LSR materials for specific performance requirements.
Design Flexibility
Allows creation of complex shapes and features with high precision, providing flexibility and durability in the final product.
Benefits for Your Application
LSIM offers precise control over dimensions and properties, making it suitable for applications where tight tolerances are required.
Design Considerations and Best Practices
When designing parts for injection molding, consider:
- Designing for manufacturability (DFM)
- Considering end-use purpose and environment
- Uniform wall thickness and draft angles
- Minimizing sink marks and voids
By following these guidelines and best practices, you can create designs that are functional, manufacturable, and cost-effective. Send us your design for a review, and we’ll provide suggestions to help you achieve optimal results.
Manufacturing Capabilities and Certifications
Our manufacturing capabilities include compression, injection, and extrusion silicone molding processes. We are committed to quality and environmental standards, as reflected in our certifications:
- ISO 9001
- ISO 45001
- ISO 14001
We comply with FDA guidelines for food-grade and skin-safe products.
Supply Chain Flexibility
We prioritize supply chain flexibility, offering on-demand manufacturing services with options for:
- Bridge tooling
- Just-in-time (JIT) production
- Standard production
- Dual-sourcing strategies